La pyramide de l'automatisation (ISA-95)
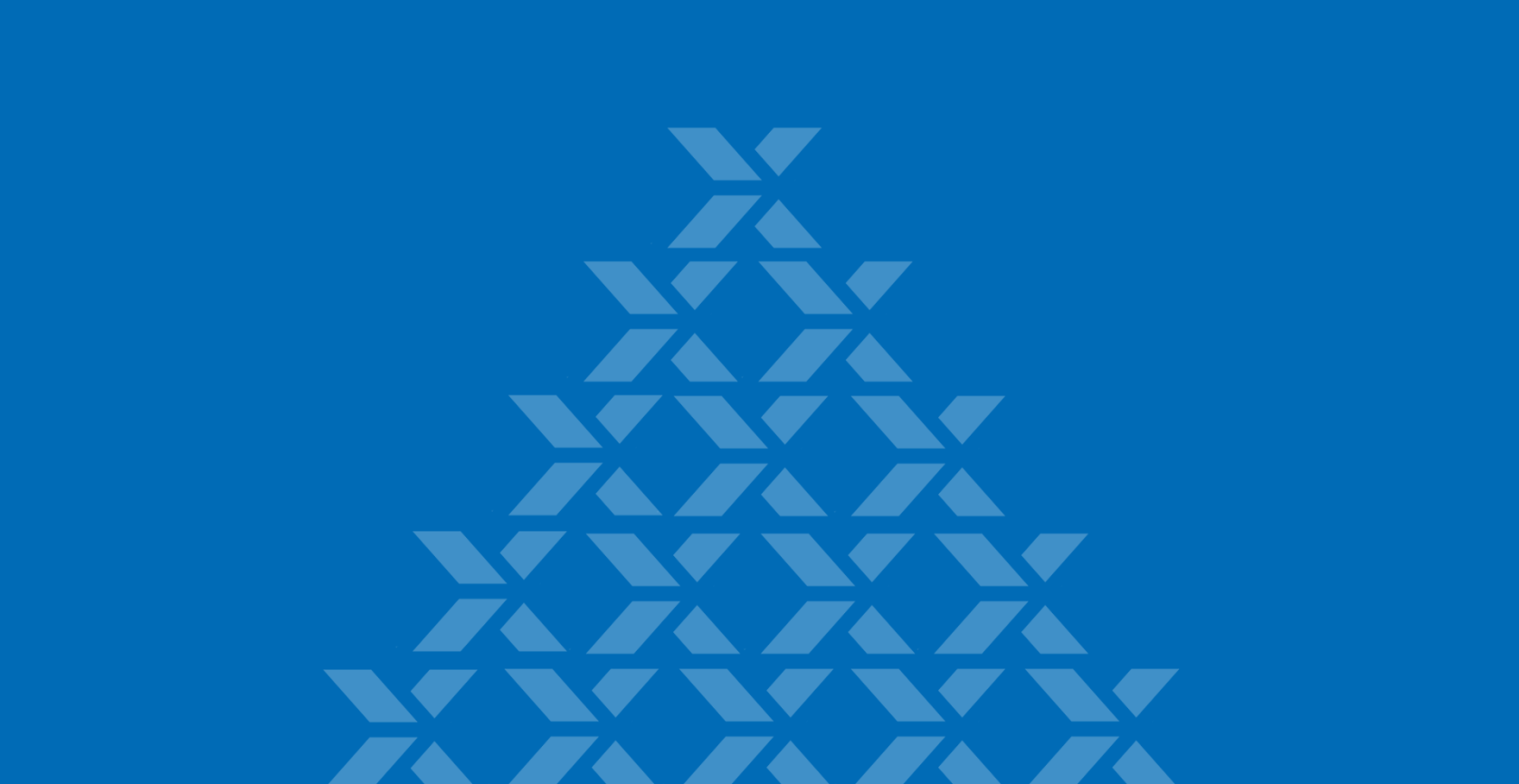
La révolution industrielle a amené des changements de paradigmes importants pour tout ce qui touche la fabrication et la gestion manufacturière. Le domaine manufacturier n’a depuis cessé de mettre en place des moyens pour permettre aux entreprises d’accroître l’efficacité de leurs opérations.
Intégrer les systèmes à ses opérations
L’intégration verticale des différents niveaux d’automatisation permet de collecter en temps réel les données provenant du plancher de production, des différentes machines et des automates programmables (PLC). Ces données sont une véritable mine d’or et, bien gérées apportent une forte valeur ajoutée pour toutes entreprises désirant demeurer concurrentielle.
Peu importe où votre entreprise se trouve en termes d’intégration et automatisation de ses processus, les possibilités sont vastes. Intégrer ses systèmes les uns aux autres apportent des avantages considérables en termes d’efficacité.
C’est en facilitant et accélérant l’échange bidirectionnel de données entre les niveaux 0 à 4 de l’automatisation que les entreprises peuvent mieux gérer leurs opérations.
La pyramide de l’automatisation
Cette pyramide présente les différents niveaux d’automatisation définis par la norme ANSI/ISA-95.
La norme ISA-95 est la norme internationale pour l’intégration des systèmes d’entreprise et de contrôle. Elle se concentre sur la définition et l’intégration des activités entre les systèmes permettant aux entreprises d’obtenir une perspective globale et ainsi prendre des décisions éclairées.
Regardons ensemble chaque niveau de la pyramide de l’automatisation pour connaître comment chacun s’intègre dans le quotidien des opérations et les avantages pour une organisation d’intégrer ses systèmes les uns aux autres.
Niveau 0 : Senseurs
Bien qu’à la base de la pyramide, le niveau 0 ne représente pas nécessairement la première étape à franchir en automatisation. C’est plutôt à ce niveau que se retrouve la quantité la plus importante de données.
Ce niveau regroupe les familles de capteurs et instruments, démarreurs intelligents et autres dispositifs fournissant de multiples données en temps réel (μs/ms). En constante évolution, ils permettent d’obtenir des données de plus en plus précises.
Plus précisément, il est question de l’ingénierie, de l’installation, de raccordement électrique, de la configuration et de la programmation des :
- Capteurs, détecteurs, analyseurs et instruments intelligents
- Lecteurs RFID et lecteurs de codes à barres
- Scanners et caméras (vision artificielle)
- Systèmes de mesure de la puissance et de la qualité de l’énergie électrique (PQM)
- Démarreurs intelligents, relais de surcharge, variateurs de fréquence et moteurs
- Vannes et actionneurs avec positionneurs intelligents
- Robots industriels et robots collaboratifs
- Systèmes de pesées (balances), systèmes de dosage, etc.
- Bus de terrain et réseaux industriels temps réel (protocoles de communication EtherNet/IP, Profinet, Modbus TCP, EtherCAT, HART, DNP3, IEC 61850, OPC UA et plusieurs autres)
Bien utilisées, les données provenant de ces objets dits « intelligents » deviennent utiles pour des buts d’analyse de la consommation énergétique, de la mesure d’efficacité globale des équipements (OEE), de la maintenance prédictive et prescriptive, etc.
Niveau 1 : Contrôle (PLC)
Ingénierie, installation, raccordement électrique, configuration et programmation de :
- Contrôleurs industriels / automates programmables industriels (PLC)
- Systèmes de contrôle distribué (DCS)
- Systèmes instrumentés de sécurité (SIS)
Il s’agit en quelque sorte d’ordinateurs industriels.
Des systèmes de contrôles de nouvelle génération sont requis en cette ère de l’industrie 4.0 pour qu’une usine demeure compétitive et à la fine pointe de la technologie. À titre d’exemple, de nouveaux contrôleurs industriels offrent des fonctionnalités d’intelligence artificielle intégrées, basées sur des réseaux de neurones, pour faire de l’analyse prédictive.
Le niveau 1 permet l’agrégation de données. Les technologies et les automates du niveau 1 intégrées, à par exemple un capteur du niveau 0, permettent de contextualiser les données de ce capteur pour ainsi leur donner un sens. Sur une chaine de production par exemple, le niveau 1 permet de détecter l’endroit où il y a un arrêt.
Niveau 2 : Interface Operateur (SCADA/HMI)
Ingénierie, installation, raccordement électrique, configuration et programmation de :
- Interfaces homme-machine (HMI)
- Systèmes de contrôle et d’acquisition de données (SCADA)
Les technologies récentes, soit les HMI et SCADA modernes, permettent la surveillance et le contrôle d’une usine entière, à partir de n’importe où d’un simple ordinateur portable et/ou appareil mobile. Les salles de contrôle munies de boutons poussoirs, de témoins lumineux, de cadrans, etc., sont maintenant remplacées par des interfaces beaucoup plus visuelles.
Avant | Maintenant |
![]() |
![]() |
En effet, l’archivage de plusieurs milliers de données à chaque seconde, ou à une fréquence plus rapide, rend possible l’affichage de courbes de tendances et l’analyse des données historiques. Les échanges de données bidirectionnelles en temps réel avec les systèmes aux niveaux supérieurs de la pyramide de l’automatisation peuvent être réalisées via de nombreuses technologies récentes (SQL, REST API, XML, OPC UA, MQTT, etc.).
Niveau 3 : Données (MES)
Ingénierie, configuration et programmation de :
- Bases de données relationnelles (telles que Microsoft SQL Server, Oracle, etc.)
- Rapports de production, rapports pour l’environnement, rapports d’évènements
- Tableaux de bord avec indicateurs clés de performance (par exemple la solution MIA d’Excelpro)
- Gestionnaires de recettes et de fabrication par lots (« batching »)
- Systèmes d’exécution de la fabrication (Manufacturing Execution System) (MES))
- Gestion de la manutention et du stockage
- Gestion de la qualité
Le niveau 3 fait référence à tout ce qui a trait à l’informatique industrielle. Il permet de procéder à la transformation numérique des PME manufacturières en éliminant de nombreux formulaires papier, fichiers Excel et applications informatique faites « maison ».
L’objectif visé est d’intégrer verticalement, avec tous les autres niveaux de la pyramide de l’automatisation, tout ce qui touche à la collecte et l’acquisition des données, l’ordonnancement de la production, la gestion du personnel, la gestion des ressources, le cheminement des produits et des lots, la traçabilité des produits et la généalogie, le contrôle de la qualité, la gestion des procédés, l’analyse des performances, la gestion des documents et la gestion de la maintenance.
Niveau 4 : Gestion (ERP)
Le niveau 4 inclut l’intégration d’un progiciel de gestion intégré (ERP) avec par exemple un logiciel de gestion de la chaîne d’approvisionnement (SCM) ou avec un logiciel de gestion de la relation client (CRM). Le niveau 4 se concentre principalement à l’intégration des systèmes utilisés lors de la gestion administrative de l’entreprise.
Concrètement, intégrer verticalement un système ERP avec les systèmes opérationnels sur le plancher de production permet d’obtenir en temps réel une vision claire de la santé des opérations afin d’orienter efficacement les décisions.
En résumé
Par analogie, nous pouvons considérer que le niveau 4 de l’automatisation, c’est-à-dire la couche IT qui touche principalement aux aspects administratifs de l’entreprise, ne représente que la pointe de l’iceberg de la transformation numérique des PME manufacturières lorsqu’on parle d’efficacité de la ligne de production.
La transformation numérique aux niveaux 0 à 3 de l’automatisation, tant qu’à elle, évoque la partie submergée de l’iceberg, considérablement plus volumineuse. D’où la représentation en forme de pyramide du modèle de la norme ANSI/ISA-95 : la base de la pyramide (niveau 0) est beaucoup plus large que son sommet (niveau 4). En effet, la quantité de données à collecter, filtrer, compiler, traiter et analyser est réellement massive à la base de la pyramide, puis s’allège à foison à chaque fois qu’elle remonte vers les niveaux supérieurs, grâce notamment à la synthèse et l’agrégation des données à chaque niveau.
L’intégration des systèmes est sans aucun doute une avenue à suivre pour toutes entreprises souhaitant diminuer les pertes de temps, mieux comprendre pourquoi telle situation survient et ainsi intervenir là et quand ça compte.
Prêt à entamer l’intégration de vos systèmes? Contactez nos experts pour discuter de votre réalité.