The 5 key components in digital transformation
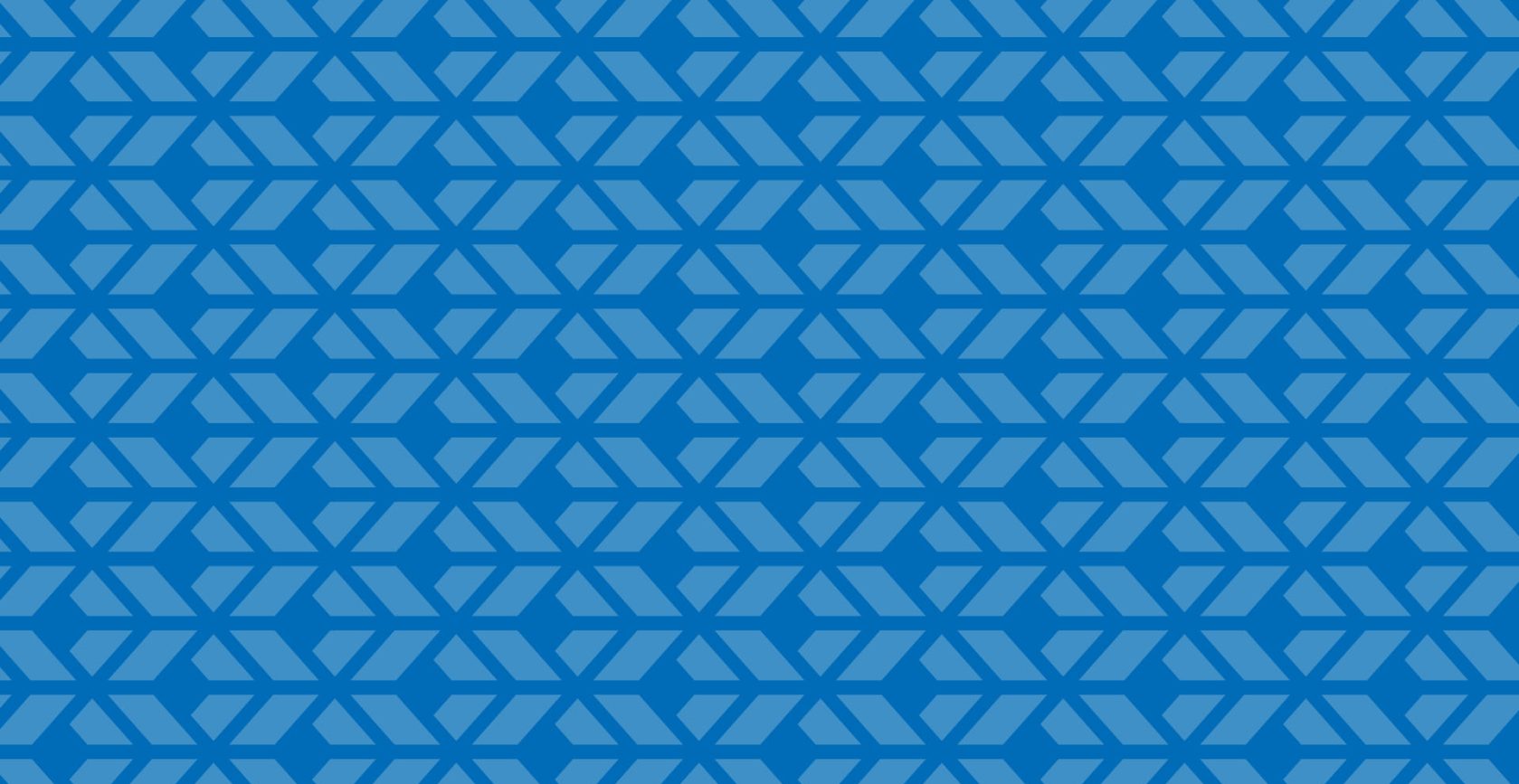
First, preparation is key
Above all, the first step in any digital transformation is a thorough analysis of the company’s specific needs. This involves understanding current processes, pain points and the objectives to be achieved or situations to be eliminated.
In short, why are you embarking on such a project?
What information are you looking for?
For example :
The ultimate goal of a digital transformation is generally to optimize production. This can mean automating specific tasks, detecting bottlenecks, improving efficiency and reducing downtime.
Understanding return on investment
It’s easy to estimate that an equipment performance optimization project improves production by an average of 10%. A quick calculation will give you the return on investment you need to manage stakeholder expectations.
For example, if this equipment is currently generating annual revenue of $100,000, and the project costs $50,000, the return on investment will be 5 years.
If the same $50,000 project is carried out on equipment earning $10,000 a year, the return on investment will be 6 months.
The results of a digital transformation project on equipment will quickly be visible on the production line, but it’s important to understand that it takes some time for the investment to be fully amortized.
Here are 5 key aspects of a digital transformation project.
Stage 1: Infrastructure
Network architecture: Having a robust network infrastructure is the key to building a solid, sustainable foundation. This involves designing and implementing a reliable, secure network capable of supporting the company’s IT and OT operations over the long term.
Audit and design: Before setting up a new infrastructure, it is imperative to carry out a thorough audit of the existing one. This helps to identify weak points and design a solution tailored to the company’s specific needs. It’s also at this stage that we get an idea of the investment cost that a digital transformation project could represent for our company.
Installation and configuration: The configuration of infrastructure components and the convergence of industrial networks are essential to ensure smooth operation.
Industrial Internet of Things (IIoT): IIoT is the term used to describe all connected devices that collect and exchange data in real time within the industrial environment. These intelligent sensors, combined with advanced communication technologies, enable more granular and precise monitoring and control of production processes. This requires a robust, scalable network architecture capable of handling the multitude of data generated by connected objects. Knowing your initial objective helps you determine the extent to which IIoT is necessary.
Cybersecurity: Cybersecurity is an element to be put at the top of the list. It is crucial to implement robust protection measures to prevent potential threats. The implementation of a demilitarized zone, better known as a DMZ network, is often recommended to isolate specific data from malware.
–> An Excelpro’s success project: A more secure network to prevent cyber attacks
Stage 2: Acquisition
Data collection: Your production line already contains a wealth of information. You just need the right tools to capture it. Several databases exist to store, organize and retrieve information efficiently.
Solution selection: Once requirements have been clearly defined, it’s time to select the right software solutions. These may include SCADA (Supervisory Control and Data Acquisition) or MES (Manufacturing Execution Systems) systems, which enable industrial processes to be monitored and controlled in real time.
Stage 3: Storage
Data security: Data security is a top priority. Strict measures must be put in place to protect sensitive information from unauthorized access.
Data archiving: An effective archiving plan ensures that critical data is kept secure and accessible.
Historization: Historization keeps an accurate record of past events. The PI historian is a powerful tool for storing and analyzing large quantities of industrial data.
Stage 4: Visualization
Data analysis: The various systems enable the configuration of dashboards and reports for clear, concise data visualization, whether locally on a computer or in the cloud. The resulting data analysis provides valuable information for informed decision-making.
Stage 5: Decision
Understand and act: Finally, setting up the right systems dedicated to data management means that the information obtained can be used to take appropriate action:
- Make real-time adjustments to production parameters
- Set alert triggers to prevent potential problems
- Implement preventive actions to improve operational efficiency
All with the aim of optimizing production, quality and equipment planning and maintenance. Artificial intelligence is increasingly used to forecast or analyze results.
In summary
A goldmine of information is hidden in data, all it takes is the right tools to capture and visualize it, safe from malware, and thus ensure intelligent, quick and accurate decision-making, boosting a company’s productivity and competitiveness. This is what 4.0 is all about.
Digital transformation is a process that requires a well thought-out approach. Each element plays a crucial role in the success of such a corporate project, and their harmonious integration is the key to success.
Ready to get started?
Contact our team to discuss your needs and objectives. Together, we’ll develop the best solution for you to access the true value of your enterprise data and take your business to the next level.